Although the commercial trucking industry has never seen anything quite like the disruptions brought on by COVID-19, the industry has overcome disturbances caused by other disasters—both natural and economic. Through the course of this health crisis and economic shutdown, commercial carriers are learning some new lessons, and many are working to become even more resilient coming out of this.
During a recent Northwestern University Transportation Center (NUTC) roundtable discussion on transportation, logistics and supply chain networks under COVID-19, 36-year trucking industry veteran Bill Matheson, president of intermodal services at Schneider National, suggested the industry take bits and pieces of lessons learned from previous disruptions and apply them today. Matheson was joined by Ben McLean, CEO of Ruan Transportation Management Systems, and Andrew T. Boyle, co-president of Boyle Transportation, for the NUTC roundtable.
In early February, Schneider spoke with shippers about interruptions accessing Asian imports. Matheson explained that at the time, shippers were concerned about supply not only because of tariffs and the trade war between the U.S. and China, but also because the spread of the novel coronavirus in China was beginning to disrupt supply networks.
“If you break down the life cycle of where we are in a beginning, middle and ending of the pandemic, I’d say we are right in the middle,” Matheson said.
“We’ve got 30 million people furloughed or out of work,” he added. “That is certainly going to have an economic impact given that we rely on consumption to drive the demand for goods.”
The big question Matheson posed is, what does the end look like?
“I think we are all confident that we are going to move through this, and some things will be different—some permanently—and some will move back to the normal that we used to know,” he noted. “But the question is how quickly? For those people who are furloughed, how quickly will they be called back to work, and have they dug themselves into a financial hole that will change their spending patterns? When they come back, will it be a snapback or a long, slow comeback?”
Lessons learned
Because of disruptions within supply networks, many end users are thinking more about how to diversify sourcing, Matheson pointed out, particularly when it comes to personal protective equipment (PPE) and other items mainly sourced from Asia. So, even if businesses have three or four domestic suppliers to rely on, those suppliers may rely on a single supplier in Asia, which can create a bottleneck.
“If there are outages with that single supplier, all suppliers will be deficient an availability of goods,” Matheson said. “I think the end users will understand an important lesson of understanding the supply chain a couple layers in, so they are protected in these sorts of scenarios. I would say that mass scramble of feeling like their inventories are depleted are behind them. Now, we’re in a much more replenished type node, so it’s less disruptive and there is less of a scramble. I would say the industry has been able to recover fairly well.”
Ruan Transportation’s McLean explained that the pandemic has shed light on the fact that the trucking industry still relies too heavily on paperwork when many processes can be digitized.
“There is still too much paperwork in all of our supply chains. Some steps that can be digitized and automated will be, so there is a silver lining in terms of how we do the work,” he said.
Ruan has also leveraged freight-tracking technology for locating and reallocating assets and to provide more real-time visibility into its overall operations.
“At a time like this, with all the disruptions, those tools allow our people a much faster ability to identify freight that is available, or identify a dedicated truck or driver to move freight,” McLean said.
Through the course of the pandemic, Boyle Transportation has enacted contactless delivery, in which all drivers are using mobile apps for proof of delivery. Boyle noted that the company established tech-enabled protocols at customer sites to minimize touchpoints for drivers.
Early on, Boyle Transportation also went through great lengths procure PPE for drivers.
“A lot of the supply chain that supports our industry hasn’t been supported adequately and drivers are unfortunately fending for themselves,” Boyle said. “That’s not the way we run business. You have to go to great lengths to make sure people know you have their back.”
Right now, Boyle noted that even competing carriers are sharing protocols and best practices, particularly when it comes to accessing PPE.
“At this point, there is only one competitor right now, and it’s not another motor carrier,” he said.
Reopening challenges, building resilience
One of the challenges around reopening the economy is that some states are opening more aggressively than others, and there are different rules to follow. Matheson noted that those differences will create major logistics challenges; however, he said he expects to see more of an economic comeback rather than further deterioration.
“I don’t have a good sense yet as to how we can get back to our previous type volumes. It really comes down to the psyche of the consumer and the economic health of the consumer,” he said. Plus, there will be additional inhibitors and concerns of being out in public and interacting with people again. Those are still the question marks, and it’s very hard to speculate.”
Boyle explained that even during the pandemic, his company hired new drivers as needed in order to build resilience.
“Are you willing to sacrifice some short-term profit in order to do things right, treat people right, and take care of your customers so on the back side of this you are well positioned? That’s the route we’ve taken,” he said.
Ruan, which is an asset-based 3PL, runs dedicated fleets and operates warehouses, and has worked to integrate all its operations with fewer touchpoints and more collaboration across the supply chain, explained McLean. He added that the goal of this integrated approach is to keep all the players in the supply chain in sync via open communication.
In terms of building resilience and helping its customers through the pandemic and its aftermath, McLean stressed the importance of maintaining preexisting levels of trust and collaboration among all partners. He added that the businesses working together to solve problems in a fair way will be better off moving forward.
About the Author
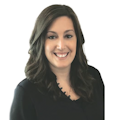
Cristina Commendatore
Cristina Commendatore is a past FleetOwner editor-in-chief. She wrote for the publication from 2015 to 2023.