Key takeaways:
- The heavy truck tire industry transitioned to radial tires in the 1980s, offering benefits like longer tread life and improved fuel economy, despite initial resistance due to costs.
- Advances such as high silica tread rubber have improved traction, durability, and rolling resistance, with regulatory demands for fuel efficiency accelerating innovation in tire technology.
- Fleets prioritize long tread life and fuel efficiency while considering acquisition costs and total cost of ownership, with choices reflecting a balance between price and performance tailored to specific operational needs.
Perhaps the greatest innovation ever in heavy truck tire technology came along in the 1980s with the introduction of radial tires. Invented by Michelin and brought into service just after World War II, they first appeared on passenger cars and commercial vehicles in Europe in the 1950s and ’60s. Radial tires took over the North American passenger car market starting in the ’70s, driven by fuel efficiency concerns and the “energy crisis.”
It wasn’t until the mid-1980s that radials became the tire of choice in trucking, especially among long-haul carriers. Radials offered longer tread life, improved handling and stability, and better fuel economy due to their lower rolling resistance.
It took trucking a while to warm up to radial tires—predictably—because they were more costly and demanded changes to long-established maintenance practices. Once the TCO became apparent, trucking went all in.
Since then, we’ve seen dozens of innovations in tire design, including some radical improvements in tread design and construction—all adding to or subtracting from the three pillars of tire performance: traction, durability, and rolling resistance.
Miles to takeoff vs. miles per gallon
Early radial drive tires were gnarly things with open shoulders and big, deep tread blocks. The deep treads offered loads of traction, and tire makers sold long miles to takeoff. Later, when fuel efficiency gained importance, tire makers reduced tread depth by a third to a half and sold the lower rolling resistance of the thinner tread. They argued that the fuel saved would offset shorter overall tire life.
Developments in compounding have enabled engineers to incorporate lower tread depths and improved fuel efficiency with enhanced traction on drives that were previously unimaginable. High silica tread rubber, for example, allowed engineers to overcome compromises between rolling resistance, traction, and wear, noted former tire designer Jim Garrett, now a product marketing manager at Michelin.
“In the past, you could make a low rolling resistance compound and still have your tread depth, for example, but it wore really fast,” he told FleetOwner. “The high silica tread proved very durable, and it offered lower rolling resistance and good traction.”
Long wear, good traction, improved fuel efficiency. Check. Check. Check.
Chalk one up for market forces.
Then, 10 or 15 years ago, the emphasis on fuel efficiency, specifically low rolling resistance, received a significant push from regulators. Meeting the evolving GHG/CAFE requirements for power OEMs had a considerable impact on the tire industry, forcing it to push the boundaries of design and development.
“Over the last several years, reductions in rolling resistance have been a primary focus for tire manufacturers,” Tom Clauer, Yokohama Tire’s senior manager of commercial product planning, said. “That focus has led to advances in compounding and unique designs. Drive tires now have lower tread depths, tighter void areas, which help reduce rolling resistance while providing the required traction and acceptable initial tread mileage.”
“For OEMs, developing a new engine is literally a billion-dollar project today," Garrett added. “So, if they can get something out of the tires, that’s almost free for them. They’ve been pushing us for years, and that’s driven some of our innovation.”
What fleets are buying today
Fleet requirements vary by operation and geography. Many fleets are now seeking fuel savings, particularly in over-the-road operations. Regional/line-haul fleets are more focused on mileage and durability, Clauer said.
“I believe the goal would be to have a product that can perform adequately in all segments, but this is only a possibility if a fleet treads lightly across segments,” he added. “The reality is each segment has unique forces to combat; choosing a tire best suited to the application will provide the best performance possible.”
Like the three pillars of tire performance, fleets weigh several cost criteria when selecting a tire: acquisition cost, cost per mile, and total cost of ownership. Acquisition cost is obvious, whereas the latter two are more challenging to tease out over the life of the tire.
“While tread wear, durability, and overhaul mileage are important considerations, for some regional operations where tires are exposed to harsh operating conditions, it’s harder to prove the value of long tread life,” Molly Chen, marketing brand manager at Maxam Tire North America, told FleetOwner. “Some regional fleets will purchase Tier 2 or Tier 3 brands at a lower price point to minimize cost per mile.”
Chen said that in more predictable applications, such as long-haul, cost-conscious fleets are looking for overall value.
“They prioritize long tread life, fuel efficiency, and consistent performance over long distances, but price is certainly a factor in the overall value/CPM equation and certainly is a priority,” she said. “Those fleets also recognize that retreading can lead to significant cost savings, and so they demand high-quality casings that can retread multiple times.”
Of course, underpinning fuel efficiency, durability, and mileage is valuable.
Along those lines, Continental introduced ContiTread HT, a fuel-efficient trailer retread for the U.S. market earlier this year, featuring an enhanced shoulder design. The tread is available across the standard sizes for various fleet applications.
“The innovative retread enhances fuel efficiency, high scrub, and offers durability,” Shaun Uys, head of Continental’s U.S. truck tire replacement business, said.
Its tread compound combines an engineered tread pattern to deliver outstanding removal mileage. Uys said the new design offers fleets up to a 20% improvement in rolling resistance, translating to lower fuel consumption and reduced operational costs.
“Fleets today are prioritizing tire selections that deliver the lowest cost of ownership through a combination of durability, performance, and proactive tire management solutions,” Chris Queen, North American technology director at Goodyear Commercial, said. “Fleet managers are increasingly favoring tires that offer extended tread life, fuel efficiency, and retreadability—helping ensure a lower total cost of ownership. But they also seek advanced technology offerings that allow them to stay ahead of tire maintenance issues before they become costly problems.”
While not directly related to tire performance, Queen said fleets are looking to align with suppliers that deliver value-added services, such as tire management programs.
“Goodyear’s comprehensive suite of tire management programs and intelligent tire solutions, including Fleet HQ and Goodyear TPMS Plus, empower fleets to be more proactive with maintenance and help uncover new opportunities to reduce costs and downtime,” Queen explained.
How did we get here?
Improving tread design, specifically, and tire design generally, has historically been a game of inches. However, the field has blown wide open over the past decade or so, primarily due to advances in simulation technology and tire-building capabilities.
“Tire manufacturers are able to run digital simulations on new tires before they are ever tested in the field, providing engineers with the insight they need to make necessary improvements to the design,” Robby Hamby, director of commercial product strategy at Bridgestone Americas, told FleetOwner. “Computer technology has also aided lab-scale validation efforts. Engineers can now understand performance impact and optimize designs in real time without running full-scale fleet validations.”
Simulation technologies allow engineers to model complex tread patterns and predict how they will perform in various conditions (wet, dry, snow, etc.). They can also simulate stress, heat, and wear on a tire before making physical prototypes.
“Advanced computer modeling and simulation have revolutionized how tread designs are developed,” Gavin Broussard, Apollo Tyres’ national sales head, said. “That has enabled the creation of tires that perform better, last longer, and meet stricter safety and environmental standards.”
Traction continued to improve with the development of precision siping—tiny zig-zag cuts in the tread face. But that required advances in tire manufacturing processes.
Michelin uses 3D-printed metal parts in the tire molds, allowing previously impossible tread designs—including advanced siping and its Regenion technology—that open up new grooves in a tire as it wears.
“You have to design those features in a way that you create the groove without creating too much demolding force,” Jim Garrett, product marketing manager at Michelin, told FleetOwner. “Otherwise, you could damage the mold, the curing press, and the tire. A lot of research went into that.”
Tire manufacturers can build tires that deliver more of what fleets look for in a tire with far fewer compromises. The 200,000-mile tire is fairly common today, with many makes and models running out to 300,000 miles and more in well-managed tire programs.
Evolving tread designs
While tire makers offer a full range of products to suit any fleet preference, their premium long-haul offerings tend to reflect state-of-the-art design and engineering. Premium fuel-efficient drive tires tend to look more like steer tires these days, with tightly packed tread blocks, distinct circumferential grooves, and closed shoulders. And they perform as well or better than the tires your uncle was buying 20 or 30 years ago.
But wait. Michelin is about to unveil a tread design that flies in the face of conventional tire designs. It launches officially in early July, but Michelin has been touring the X Line Grip D to trade shows and dealer events. It always gets a strong reaction.
It’s built on a brand-new casing design that incorporates existing technology, which engineers have refined and improved. But it’s the tread design that gets people’s attention.
Garrett says they are seeing 20% more miles from the tire overall, but due to the chevron shape of the grooves, the compound, full-depth siping, and the new siping layout, end-of-life traction is off the charts.
“We’re equal to or better than the XDN 2 when new, but we crush it at the worn stage,” he told FleetOwner. "We’re getting 90% better snow traction at the end of life than the very popular XDN 2.”
The XDN 2, after 22 years, remains Michelin’s most popular tire. Garrett said they decided not to try making incremental improvements to that tire but rather start with a clean slate and incorporate all the learnings from that tire while bringing a lot of new technology to the design.
And that is how tread designs and tires evolve as a whole. Your Uncle Floyd would be astonished at the progress we’ve made in tire design since the radial first came to market.
About the Author
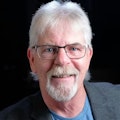
Jim Park
Jim Park is an award-winning journalist who has covered the trucking industry since 1998. Before that, he racked up 2 million miles as an over-the-road truck driver and owner-operator pulling tank trailers. He continues to maintain his CLD. Park's previous driving experience brings a real-world perspective to his work.