A lot may have changed since 2004, but at Blue Dot Readi-Mix some things have stayed the same. Then and now, the locally owned company headquartered in Mint Hill, North Carolina, has taken an approach to meeting customer needs that has led to solid relationships and an expanding customer base.
Applying that same dedication to the company fleet of 125 mixers also has resulted in highly reliable and productive equipment. The current fleet at Blue Dot consists of Kenworth T880, Peterbilt Model 365, and Peterbilt Model 567 trucks.
“With the ability to invest effectively in equipment, we’re able to set a trade cycle so we’re operating the latest and most cost-effective vehicles,” said Jason Spangler, fleet manager. “We have a five-year rotation plan, which we implemented in early 2020, and our growth now has us ahead of our targeted date of completion.”
In 2020 as well, Blue Dot switched to Paccar MX-13 engines and with its replacement plans all of the company’s trucks will have either MX-13 or MX-11 power. Historically an all-manual transmission fleet, the company also began spec’ing Allison 4500RDS automatics to help attract more drivers, and for their higher trade value.
See also: When is the ideal time to replace an asset?
Maintenance and common mixer and chassis repairs for the Blue Dot fleet are handled primarily in-house by five mechanics at a network of company shops that service equipment domiciled at seven concrete plants.
“Reliability is absolutely essential in our business,” Spangler stated. “Not only are customers depending on us to deliver on time, but if a truck breaks down, the concrete sets and we have to replace a very costly drum."
“One of the things that has helped ensure uptime is a triage program we started back in 2021,” he explained further. “With the program, our lead mechanic triages trucks 50 to 100 engine hours prior to their next PM window. Before that, we had multiple trucks going into shop locations for service with no idea what repairs would be needed to get them back on the road quickly."
“Triaging trucks early gives us time to identify repairs, find parts—especially when the pandemic causes major supply chain constraints on availability—and deliver a detailed work order to our mechanic before the truck shows up at the shop,” Spangler continued. “It didn’t take long before our turnaround time on repairs greatly improved, and it’s still getting better.”
See also: The post-pandemic parts plan: Distributor and supplier solutions
Blue Dot also uses technology to improve uptime. In particular, Spangler pointed out, are the remote diagnostics capabilities of the Kenworth TruckTech+ Service Management System. “Issues happen,” he said. “TruckTech+ lets us anticipate what’s going to happen by providing real-time data on fault codes. That improves our response time to truck down issues, and it helps us build a data set of common fault codes and repairs so we can know in advance what can happen and be ready.”
For fleet, maintenance, and driver management, Blue Dot is leveraging other technologies as well. All historical work order data is housed in eMaint Computerized Maintenance Management System software, which is used to create a predictive maintenance model for the fleet. The Coretex 360 Tracking & Fleet Management System provides telematics, PM scheduling, and job cost analysis capabilities. Additionally, Samsara is providing an onboard camera solution that is used to score driver behavior and improve training.
The Blue Dot maintenance operation also relies on Paccar Davie 4 and Cummins Insite engine diagnostic software. “These tools have been invaluable in our triage program for building a set of common fault codes and what it takes to resolve them,” Spangler explained. “They have also improved our hand-off of trucks to dealers once we determine if a repair is outside our scope of work."
“Part of our fleet purchase changes in 2020 included adding engine and aftertreatment system warranties to minimize our repair costs,” he added. “These tools allow us to determine, to a degree of certainty, if the repair will be covered by warranty or not before we send the truck to a dealer for service.”
Anticipating needs and applying the best tools to address them is a proven formula at Blue Dot Readi-Mix. By using that approach to fleet management, it is helping drive growth and maintain high levels of customer service.
About the Author
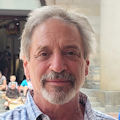
Seth Skydel
Seth Skydel, a veteran industry editor, has more than four decades of experience in fleet management, trucking, and transportation and logistics publications. Today, in editorial and marketing roles, he writes about fleet, service, and transportation management, vehicle and information technology, and industry trends and issues.