Valley Proteins is a successful company specializing in a unique type of freight. Used restaurant cooking grease, fats, oils, restaurant grease traps, inedible meat, fat, and bone by-products are part of the daily loads hauled by the company’s private truck fleet. To meet the challenges of this specialized service, the fleet consists of 455 drivers; 416 company-owned Class 8 power units; 969 dump, tanker, and hopper trailers; and 22 Class 7 power units based at one of the company’s 23 facilities.
“We provide prompt disposal for some 50,000 customers, including chain and independent restaurants, supermarkets, poultry processions plants, abattoirs, and food service institutions,” says Richard Evans, CTP, director of transportation. “In addition to recycling some of these by-products into high-energy feed fat and protein-rich animal feeds, we have begun producing biofuels from these recycled animal fats.
“Our turnkey process begins by providing each store with properly sized, leak-free containers to fit the volume generated by each location,” Evans explains. “We empty the containers, always in compliance with the most current government regulations, and replace any damaged containers with new ones. We maintain very high standards for recordkeeping to document our compliance with ever-growing environmental regulations.”
What are some of the company’s greatest challenges? “Theft,” Evans says. “Grease theft from our on-site customer containers is becoming a major problem for us and the industry overall. Also, the lack of firm quantities of day-to-day volume that we pick up and wide disparities in service frequencies make the logistical puzzle of our work very complex.”
Driver retention is a challenge as well due to the special nature of the work demanded. Drivers have to roll containers and barrels, which are subject to spillage. Some drivers have to rake out feathers to even out the load before applying the tarp. Much of the driver’s job is done after hours, under the cover of darkness; in fact, at least half of the driver’s job involves non-driving tasks.
“Our turnover is around 25% annually,” says Evans. Several changes are in place to reduce turnover such as activity-based pay incentives to increase productivity, which should result in fewer, more qualified drivers that are paid a higher wage. Next-generation onboard computer technology now gives drivers the tools to work smarter and more efficiently with customers to grow business volume and optimize loads.
Training has been institutionalized with the transportation team. “Developing talent within our organization is a key component of building a first-class operation,” says Evans. “That’s why Valley Proteins identifies one candidate a year to attend the Private Fleet Management Institute and sit for the CTP examination. In fact, attaining the CTP designation has now become a prerequisite to advance through the management ranks.”
“I’ve held my Certified Transportation Professional credential for 17 years. It has been one of the best investments of my career,” says Evans. “I hope many others at Valley Proteins can follow in my footsteps.”
About the Author
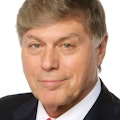
Gary Petty
Gary Petty has more than three decades of experience as a CEO of national trade associations in the trucking industry. Since 2001, he has served as president and CEO of the National Private Truck Council, the national trade association founded in 1939, representing the private motor carrier industry. Petty is the Private Fleet Editor and columnist for FleetOwner, where he writes monthly articles about successful managers and business models in the private fleet market.