Across the entire operation at Sunrise Transport, everyone from senior management to drivers to the shop team understands the critical nature of delivering perishable products, said Greg Goss, vice president and general manager.
“Our fleet is a differentiating factor in our success, and a delivery operation that is second to none is a big selling point,” Goss stated. “That’s why we have a full-service shop to provide timely and efficient service.”
The family owned private fleet of Four Seasons Produce Inc. fields about 100 Freightliner Business Class trucks and Cascadia day cab and sleeper tractors, along with Great Dane and Utility trailers. Based in Ephrata, Pennsylvania, the company is a wholesale produce distributor serving organic markets, co-ops, independent retailers, and chain stores in the Mid-Atlantic and Northeast regions.
It also harvests new technicians from its crop of maintenance assistants to help keep its trucks and reefer trailers running
“We implemented a ‘Grow Your Own’ program a couple of years ago,” Goss said. “We hire fuelers and washers who may be going to school to become technicians, and when there is an opportunity, we promote them to junior technician. After training, their primary responsibility is to complete preventative maintenance 60% of the time, and the other 40% is allocated to working side by side with an experienced technician.”
Sunrise Transport also has a full-time trainer who works with every new technician, regardless of experience, on shop and company processes and procedures. The training lasts from four to eight weeks, depending on the technician’s experience and ability to retain and follow information.
Another successful company approach to recruiting technicians is to partner with a local technical school that has a program for diesel technicians. “We’ve hosted visitation days where students rotate through various stations in our shop to help attract the best and brightest students,” Goss said. “We also offer our trainer to teach a class and we have donated a truck that we retired from our fleet and a refrigeration unit to the program.”
Goss noted that Sunrise Transport often has found that diesel technicians can be harder to find than drivers. As a result, it has developed unique approaches to recruiting the help it needs.
“The fleet has to be ready at all times to make next-day deliveries of fresh produce and perishables to hundreds of customers,” Goss said. “It takes our shop management team—15 technicians who cover three shifts per day, six-and-a-half days each week, six fuelers and washers on two shifts daily, and parts personnel—to make that happen.”
Goss also pointed out that the Sunrise Transport shop staff is not only responsible for maintenance and repairs on trucks, tractors and trailers. They also provide service for a variety of Carrier Transicold refrigeration unit models, Maxon liftgates, and several makes of APUs that are specified for sleeper-equipped power units.
Freightliner of Lancaster, Sunrise Transport’s local dealer, also has a technician based at the fleet’s shop to handle warranty work. That also means the company doesn’t have to use its own staff to move trucks back and forth between facilities. For any major body work, trucks and tractors are sent to the Freightliner dealer’s body shop; trailers go to local Utility or Great Dane dealers.
“There are several reasons we partner with these vendors, including quality of work, accountability for worked performed, and completing repairs quickly to reduce downtime,” Gross said.
Sunrise Transport employs a full-time associate dedicated to parts and tire inventory. The fleet, which negotiates pricing based off volume, has some parts on consignment and participates in national purchasing and rebate programs offered by suppliers.
The full-service Sunrise Transport shop has four drive-through bays, one bay with a pit and one with an auto lift, as well as a wash bay with an automated system and a two-lane fuel island.In the shop, technicians have access to a wide range of OEM diagnostic software from Freightliner, Cummins, Detroit, Allison, Eaton, Thermo King, Carrier, WABCO, Bendix and Haldex. It also utilizes on-board technology for proactive monitoring such as Detroit Connect Virtual Technician, systems from Peoplenet, and ORBCOMM solutions for refrigeration units.
For managing its service operation, Sunrise Transport has deployed Trimble TMT Fleet Maintenance software. Its shop managers use the solution to review repair orders for accuracy and to see how labor time compares to established SRTs. Technicians use the software to create repair orders, record labor time and parts, and they can review unit information, including specs and repair histories.
TMT also generates a series of reports on costs, including repairs by VMRS code, technician productivity, downtime, PM currency, breakdowns, parts and tire inventories, and warranty recovery. “These metrics detail where we need to focus attention,” Goss said. “We use data trends to identify patterns and find opportunities to help support the mission of Sunrise Transport—to provide on time deliveries to customers with reliable equipment.”
This article originally appeared on Fleet Maintenance.
About the Author
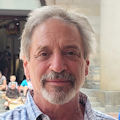
Seth Skydel
Seth Skydel, a veteran industry editor, has more than four decades of experience in fleet management, trucking, and transportation and logistics publications. Today, in editorial and marketing roles, he writes about fleet, service, and transportation management, vehicle and information technology, and industry trends and issues.