Gaining efficiency. That’s what Jason Roell, shop manager at Crum Trucking, said is top of mind for the Batesville, Indiana-based dry van truckload carrier’s maintenance operation.
“It stems from striving to have every one of our 18 technicians do the jobs they are assigned a specific way, especially tasks like [preventive maintenance],” he explained further. “Once someone has a good routine, efficiency and quality increase.”
But Roell also was quick to point out that there’s often nothing routine about a trucking operation, especially one like Crum’s, which services more than 160 tractors and 400 trailers from its central location in southern Indiana to multiple destinations throughout the U.S., Canada, and Mexico. And more than 80% of those runs are dedicated to specific customer needs.
In Crum’s widespread operation, challenges always arise, and it takes the fleet’s 24/7/365 maintenance team to make sure the equipment is always ready to roll. They do that in several ways at a newly built, state-of-the-art shop with six pull-through service bays, and an inspection bay that each combination goes through when returning from their run. The shop also services trucks operated by the carrier’s independent contractors.
See also: Asset health checks help fleets make the right decisions
“Our inspection bay has a different purpose than one in a dealership that has what they call a ‘quick lane’ or something similar,” Roell related. “If any repair or diagnosis takes more than 25 minutes or so, it is performed in another bay.
“Our inspection bay’s purpose is to inspect every truck and trailer when they enter the yard,” he continued. “It’s intended to be a quick inspection of about 10 minutes or less between the driver and technician to look for [Department of Transportation] items or anything that may potentially cause a breakdown.”Beyond that first stop in the shop, Crum has three bays that are used for anything from changing kingpins to a differential in a rear-end. Another bay is fitted with lifts and is used primarily for PMs, but other jobs, such as pinion seals, often are performed on the lifts as well to save time. There is also a bay where most trailer and tire work is performed, but it is not limited to that use; another houses a drive-through truck wash.
Time and efficiency also are factors in decisions at Crum’s shop to outsource more complex tasks, such as overhauls. For those items, the carrier uses dealers and distributors, who also take care of repairs covered by the warranty. Those outfits are chosen by the quality of work, customer service, and competitive price comparisons.
“The same goes for the independent shops we use to service some trucks and trailers that are domiciled away from our home terminal,” Roell added. “Other factors in that decision include choosing facilities on our routes while we also have parking agreements with some of them.”
Driving maintenance efficiency at Crum Trucking as well is a focus on parts purchasing and management. Dealers and distributors are the fleet’s primary suppliers. They are chosen carefully, Roell said, along the same lines as the mindset for picking outside service vendors who have proven to deliver. Additionally, they have purchasing platforms, and many offer national accounts programs so pricing is the same anywhere in the country.
Organizing tools and parts
“To keep downtime for service to a minimum, we keep a supply of frequently used parts in our inventory,” Roell related, “and we track lifespans so we can determine the best time for a replacement. At the same time, organization of parts in our shop is key to being efficient and productive. For example, engine filters are next to the PM bay, and all fluids are dispensed using a bank of reels.
“We take the same approach to tools,” Roell added. “Equipment such as jacks and jack stands have designated places marked on the floor for when they are not in use. Shop tools in the tool room are organized, some with foam cutouts of the tools in the toolbox drawers. There are also workbenches in between every other bay.”
See also: Technician training in the digital age
What Roell said is perhaps most important for making sure that Crum Trucking’s fleet is safe and in good working condition are well-trained and committed technicians, who he calls “the heart of our maintenance operation.”
To that end, new employees are trained by senior technicians, and the entire staff is taught by instructors from parts and service suppliers and manufacturers. The training covers specific procedures and the latest tractor and trailer systems and components.
“We make sure everything is operating as efficiently as possible in our shop by tracking things like the amount of time for specific work, and we communicate reasonable time limits to technicians,” Roell stated. “But while time is measured, accuracy is more important. Speed doesn’t matter if it results in rework; not sacrificing efficiency is the real key to keeping equipment moving for our customers.”
About the Author
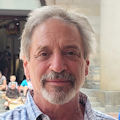
Seth Skydel
Seth Skydel, a veteran industry editor, has more than four decades of experience in fleet management, trucking, and transportation and logistics publications. Today, in editorial and marketing roles, he writes about fleet, service, and transportation management, vehicle and information technology, and industry trends and issues.