Uncovering the hidden costs of truck idling that eat away at your bottom line
It is a given in our world of transportation and logistics that managing a fleet of diesel trucks requires constant attention to operational efficiency and cost management. Inattention to these two pillars can negatively impact your fleet's overall health and the company’s sustainability initiatives.
One primary factor significantly impacting a fleet's bottom line is the cost associated with diesel truck idling. While it may seem like a necessary evil to maintain cabin temperatures and power small appliances and electronics inside, it comes with many hidden costs that can eat away at your bottom line.
Fuel consumption
According to the North American Council for Freight Efficiency and customer feedback, an idling engine significantly increases fuel consumption, burning an average of 1 gallon of fuel per hour.
Assuming an average hourly fuel consumption of one gallon during idling for a heavy-duty truck, a fleet of 100 trucks idling for six hours daily would incur a daily fuel expense of 600 gallons. This translates to an annual consumption of 180,000 gallons (considering 300 operational days).
At an estimated fuel cost of $4 per gallon, this fleet's annual idling fuel cost reaches $720,000.
Consider your fleet size and the direct hit this causes to your operating budget.
Engine wear, tear, and more maintenance
Truck idling isn't just a fuel waster—it's an engine wrecker. The American Trucking Associations reports that idling can cause one hour of wear and tear to be equivalent to three to six hours of highway driving due to incomplete fuel combustion. The buildup of carbon residue harms engine performance and shortens lifespan by hindering spark plugs and damaging exhaust systems.
Soot buildup clogs Diesel Exhaust Fluid filters and Diesel Particulate Filter systems, reducing efficiency and requiring more frequent cleaning or replacement. Additionally, lack of proper oil circulation during idling accelerates wear on internal components, leading to more frequent and expensive maintenance needs. The cost? An estimated $0.15 per hour in maintenance for every hour of idling, based on a National Research Council report.
In short, idling equals more maintenance headaches and a shortened engine lifespan.
See also: Clark: Fixed cost is a good reason for fleets to lease rather than buy
Idling fines
Idling can also lead to financial penalties for drivers. Although New York has become notable for implementing strict idling restrictions, over half of the states now have restrictions. Violating these regulations can result in hefty fines, adding a layer of unexpected cost to operations.
Furthermore, these restrictions limit where truck drivers can legally park and idle. This can disrupt schedules and make it challenging to take mandated breaks or wait for deliveries in designated zones. The combined effect of fines and limited idling locations can add hidden costs and inefficiencies to trucking operations in regulated areas.
Driver rest
Idling trucks generate noise that can disrupt required driver rest periods. Auto start-stop systems, while promoting fuel efficiency, can also interrupt sleep cycles with their jarring on-and-off cycles. These disruptions can contribute to driver fatigue and decreased alertness, potentially compromising safety and leading to lower driver retention rates in the long term for fleets.
Choosing a solution to minimize hidden costs
Idling poses a financial burden on fleet operations through increased fuel consumption, additional maintenance costs, and accelerated engine wear. By implementing strategies to minimize idling, fleets can achieve significant cost savings.
About the Author
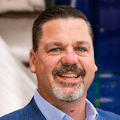
Wade Seaburg
Wade Seaburg is the chief revenue officer at Dragonfly Energy, where he leads sales, business development, and revenue growth and diversification efforts. He is an industry veteran who has proven long-term success serving high-volume OEMs across various markets.