Transforming fleet maintenance from cost center to strategic advantage
Key takeaways:
- Shift from reactive maintenance to a proactive approach that uses data to anticipate breakdowns, reducing emergency repairs and improving efficiency.
- Integrate telematics and maintenance systems to leverage data for better scheduling and resource allocation through advanced analytics.
- Foster a culture that values data-driven decision-making by training staff to enhance fleet performance and reliability.
Fleet maintenance remains a reactive cost center for many—fixing equipment only after something breaks. However, with maintenance costs increasing by 12% year over year, carriers simply can't afford to view maintenance as just a cost of doing business. With tight margins and on-time delivery demands creating constant pressure, taking a predictive, proactive maintenance approach can transform the function into a strategic competitive advantage.
The strategic value of proactive fleet maintenance
Transportation fleets generate massive amounts of data through telematics, ELDs, maintenance systems, and driver reports. Yet most carriers only scratch the surface of this data's potential, tracking basic metrics in disconnected systems rather than creating a comprehensive view that enables truly predictive strategies for fleet maintenance.
While controlling costs and increasing efficiency are still essential, the most significant opportunities for maintenance optimization in transportation come from three key areas:
- Predictive breakdown prevention: Anticipating component failures before they strand drivers with loaded trailers avoids the cascading costs of roadside breakdowns: missed delivery appointments, emergency repair premiums, towing expenses, and the operational chaos of rerouting freight and reassigning drivers.
- Intelligent resource allocation: Smart scheduling of maintenance during natural operational downtimes, ensuring the right technicians with appropriate skills handle specific repairs, and prioritizing work on high-revenue units all contribute to maximum fleet utilization and uptime.
- Strategic asset lifecycle management: Transform maintenance from a necessary expense into a value multiplier by extending tractor lifespans, timing replacements to optimize total cost of ownership, and ensuring every repair dollar delivers maximum return on investment.
Reactive vs. proactive: Where does your fleet stand?
When companies view maintenance purely as a cost center rather than a strategic function, they often operate in a reactive manner. Conversely, companies recognizing that maintenance can strategically contribute to business performance take proactive approaches.
Signs you're operating in a reactive mode
- CSA violations or roadside breakdowns primarily trigger maintenance.
- Unexpected equipment failures regularly disrupt delivery schedules.
- PM schedules are based strictly on calendar intervals rather than actual usage patterns.
- Emergency roadside repairs consume a high percentage of the maintenance budget.
- Dispatch is constantly struggling with equipment availability and reliability.
- Parts are ordered only after failures occur, extending downtime.
- Systematic analysis of fleet failure patterns across makes, models, and components has not been conducted.
Signs you're taking a proactive approach
- Maintenance scheduling is driven by predictive analytics and real-time condition monitoring.
- Potential failures are addressed during planned shop visits before affecting operations.
- Root cause analysis provides insights that drive targeted fixes and long-term reliability.
- Resource allocation is optimized through integration with freight planning systems.
- Maintenance strategy aligns with business goals and customer service requirements.
- Strategic parts inventory management is based on failure predictions.
- Decision-making is data-driven across the maintenance operation.
See also: Product Spotlight: 2025 diesel additives
Building a proactive maintenance strategy for transportation fleets
To transform fleet maintenance from a cost center into a competitive advantage, transportation companies need a deliberate, data-driven strategy focusing on four key priorities:
1. Establish a strong data foundation
Everything starts with reliable, comprehensive data. Invest in proper data governance practices that ensure quality and consistency across systems. Create a single source of truth that integrates maintenance records, telematics data, driver reports, and operational metrics to give teams a shared understanding of asset health, performance, and value.
2. Integrate key systems
Break down silos between telematics, ELDs, maintenance software, and transportation management systems. Connect real-time equipment data with maintenance operations and link operational context (routes, loads, schedules) to asset condition. This comprehensive view helps enable the shift from reactive repairs to proactive planning.
3. Consider implementing advanced analytics
Once data and systems are connected, advanced analytics can unlock their full potential. Predictive failure models can flag issues before they cause road breakdowns or service failures, and performance dashboards offer visibility into trends, patterns, and inefficiencies. Implement real-time decision support systems that help teams prioritize effectively—minimizing downtime, maximizing utilization, and driving continual improvement.
4. Nurture a data-driven maintenance culture
Technology alone won't drive change. Building a culture that values data-driven thinking is essential. This means training technicians, drivers, and managers on how predictive tools work; embedding collaborative decision-making into daily workflows; and regularly reviewing models to improve accuracy.
The bottom line for transportation providers
The actual value in fleet maintenance goes beyond reducing repair costs. When fleet maintenance can prevent service failures through intelligent integration and analysis of maintenance data, it can achieve unprecedented levels of equipment reliability, operational efficiency, and ultimately, customer satisfaction.
Carriers can no longer afford to view maintenance as just a “cost of doing business.” The question isn't whether to invest in predictive maintenance, but how quickly transportation providers can transform reactive practices into proactive, data-driven strategies that create a competitive advantage.
About the Author
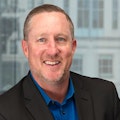
Carl Lowgren
Carl Lowgren is a fleet optimization advisor at Resultant, a technology and data consulting firm. Lowgren’s experience spans multiple industries, including transportation, energy, retail, and technology.