How to maximize fleet savings through data optimization
Key takeaways:
- Minor adjustments, such as reducing costs by 2 cents per mile, can result in thousands of dollars in savings per truck over its lifetime.
- Utilizing accurate data from various sources helps fleets improve visibility, enabling informed decisions and targeted operational enhancements.
- By identifying high-cost assets, operators can optimize maintenance and educate drivers to improve fleet performance.
Fleet operators today are navigating an increasingly complex and costly environment. With fluctuating fuel prices, tightening margins, unpredictable freight volumes, supply chain disruptions, and mounting pressure to improve efficiency, every dollar counts more than ever.
In this environment, finding ways to reduce costs without compromising performance is no longer a competitive advantage—it’s a necessity. Fortunately, even minor operational improvements can yield major financial gains when applied across an entire fleet.
The power of small changes for big savings in fleet management
Operating a truck fleet involves various costs, including capital equipment cost, fuel, maintenance, compliance, safety measures, and technology investments. Even marginal savings per mile can accumulate into substantial financial benefits when applied across an entire fleet. This scalability underscores the importance of efficiency in every operational aspect.
See also: Your next fleet manager could already be on staff
If you’re not sure small changes can lead to significant savings, consider this: A modest reduction of 2 cents per mile across 100 tractors running 100,000 miles over a five-year life cycle translates into substantial savings of $1,000,000. Consistently applying small optimizations across the fleet yields a compounding effect on cost reduction.
Comprehensive, accurate data is the key to unlocking fleet efficiency
But here’s the problem. Without data, it’s impossible to manage what you can’t see. Unfortunately, many fleets operate with limited visibility into the actual performance and cost of individual units.
High-performing fleets rely on multiple sources of accurate, granular data, including the following:
- Telematics and fuel management: Real-time GPS, engine performance, idle time, and driver behavior, as well as monitoring mpg and identifying fuel-wasting habits
- Maintenance: Leveraging VMRS (Vehicle Maintenance Reporting Standards) for consistency
- Utilization: Capturing usage frequency, trip length, and route assignments
- Fleet inventory: A complete list of vehicle specs, age, financing terms, and service history
When combined and analyzed, these data sources provide operators with visibility into the actual operating cost of each truck, enabling smarter decisions on maintenance, utilization, routing, and replacement.
Identifying the causes behind elevated costs
Not all trucks operate in the same manner. Some assets perform better, last longer, and cost less to run. Some are consistently more expensive and less reliable. Those assets need to be identified and their issues addressed.
Fleets should track key indicators to identify problem units by examining factors such as financing costs, fuel consumption, maintenance frequency, unplanned downtime, tire wear, utilization, and idle time, among others.
By identifying trends and outliers, operators can take targeted action on the highest-cost vehicles. It’s essential to note that high-cost trucks are typically expensive for a reason or multiple reasons. Common root causes include:
- Poor fuel economy due to driving style, terrain, mechanical issues, or specifications
- High maintenance and repair costs stemming from specific component failures or poor service schedules
- High monthly fixed costs from inefficient lease or financing terms
- Inefficient utilization due to poor routing or seasonal mismatch
- Wrong life cycle stage due to holding onto trucks too long or replacing too early
- Driver behavior, such as harsh braking and extended idling
When you know the “why,” you can take the “how” into action.
Turning insights into actionable strategies
Data only delivers value when it leads to action. Consider these steps to turn insights into operational improvements:
- Review financing and leasing structures: Compare fixed costs against asset performance, then refinance or restructure leases when appropriate.
- Prioritize preventive and predictive maintenance: Use historical data to anticipate failures before they happen. Address recurring issues on specific makes/models.
- Rotate routes to extend asset life: Avoid overusing your top-performing trucks while assigning less strenuous routes to older units.
- Reassign or remarket underperforming assets: Sell or trade in consistently high-cost assets. For underused trucks, consider shifting them to better-suited routes.
- Educate drivers on fuel-saving behaviors: Let them know they can help the company’s bottom line by reducing both idle time and harsh braking, among other driving practices.
Ongoing success requires continuous monitoring and adjustment. There is no guarantee that what works today will work next quarter. Data should drive regular reviews and timely responses.
Success relies on fleet operators being able to look beyond averages and instead examine per-truck performance, modeling the data to identify opportunities within the fleet.
About the Author
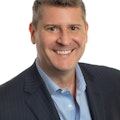
Frank Bussone
Frank Bussone, CTP, is VP of technology & data analytics, at Corcentric Fleet Solutions. With 25 years’ experience in business analytics and business intelligence, he works with the data associated with fleet operations to find efficient and lower cost solutions for truck fleets across the country.