The benefits of diagnostics are clear to Jerry Greiner, VP of business operations, procurement & fleet management at Transervice. “The data will give you an overall picture of the truck’s health and can help detect issues early before they become major problems,” he said.
“Diagnostics can also help focus your efforts on making the correct repair,” he added. “And having the data in maintenance software will benefit future technicians working on the truck by showing the history of repairs that were made.”
Chevin Fleet Solutions, a FleetWave fleet management software provider, noted that while advances in telematics mean fleets can gather more information, combining the data with a fleet and maintenance management system is a good way to use diagnostic information better.
“This way, fault codes can be raised as defects and resolved before any serious issue or downtime occurs,” the company pointed out. “Integration lies at the heart of any good enterprise-level fleet information system, and there are a huge range of benefits to be gained from integrating telematics.”
Selecting the right tools
“When it comes to diagnostic tools, it’s important to select one that offers consistency across your entire organization,” Jason Hedman, product manager at Noregon, said. “If your intake and triage technicians scan the vehicle and generate a report, then your repair technicians should have the same software and be able to view the same reports and information once connected to the vehicle.”
“Vehicle data is critical during the diagnostic process due to how many electronic components and sensors are on today’s trucks,” Hedman continued. “If you rely solely on dash lamps and visual inspections for diagnosis, then you’ll see a lot of return visits with issues that should have been caught the first time.”
In the future, Noregon expects tighter integration between diagnostic tools and shop management software to streamline tasks like work orders and invoicing, he explained. “We also anticipate continued growth in remote diagnostic usage via telematics services, which brings important real-time health and safety information into fleet management software,” Hedman added.
Asking the right questions
Brian Mulshine, senior director of product management at Trimble, pointed out that during vehicle check-in, it is crucial to view fault codes so you can better understand the questions to ask the driver. “For example, is the driver experiencing any symptoms related to the indicated fault code?” he explained further.
Mulshine also noted that fleets are seeing more codes that could result from required software updates from a component manufacturer rather than an actual component failure or malfunction needing servicing. “There are more than five computers on a truck today broadcasting over 2,000 fault codes, but it’s important to note that many of these are simply informational,” he said.
“Diagnostic data can, in many cases, help a knowledgeable maintenance manager determine proper and effective actions,” Mulshine continued. “Some examples of this could be an active code that causes an engine derate condition, or the number of times a fault code has come up could point to the severity of the issue. Some codes like low oil pressure or coolant temperature would inform the driver to stop immediately to prevent catastrophic engine failures.”
Integrating with manufacturer platforms
Manufacturers’ integrated diagnostic and management solutions include the SRM Case Estimator for Uptime Pro from Daimler Truck North America. The solution connects the Decisiv Service Relationship Management and Uptime Pro dealer service management platforms.
The Decisiv-DTNA integration streamlines estimate creation and approval processes by incorporating diagnostics, repair information, and photos from DTNA’s Express WriteUp mobile app into an SRM Case service event. The SRM Case Estimator for Uptime Pro is also integrated with Dealer Management System software and interfaces with DTNA’s Online Warranty Link system and its VIP truck specs database.
Available at hundreds of dealers is the Decisiv SRM Connector for the Cummins Guidanz servicing technology suite. The integration of Cummins Guidanz in the Decisiv platform incorporates critical asset repair and diagnostic information into a service event in the SRM Case management application. It provides technicians with real-time access to proven Cummins expertise at the point of service.
Connecting diagnostic and service management systems
The recently introduced integration between Diesel Explorer Pro diagnostic software from Diesel Laptops and the Decisiv SRM platform facilitates diagnostic scanning and automated service case creation.
“By integrating Diesel Explorer Pro with Decisiv’s SRM platform, we’re helping repair facilities and fleets eliminate time-consuming data entry, accelerate repair decisions, and get trucks back on the road faster,” Tyler Robertson, CEO of Diesel Laptops, said. “This partnership is all about reducing downtime and improving efficiency for everyone involved in the service process.”
The Decisiv integration with Diesel Explorer Pro automates case creation and updates from diagnostic data. Diesel Laptops offers the solution as part of a diagnostic software subscription. Diesel Explorer reads all diagnostic trouble codes and faults from standard vehicle modules. A paid option allows for bidirectional commands such as diesel particulate filter regenerations or aftertreatment resets and the ability to detect emissions tampering with Detroit, Cummins, and International engines.
“Diagnostic data captured through Diesel Explorer Pro is automatically transferred into Decisiv’s SRM platform, which eliminates the need for manual data entry, reducing errors and increasing accuracy,” Kyle Cooper, managing director of SaaS at Diesel Laptops, explained. “The system instantly gathers information, including the VIN, mileage, and fault codes, which helps service advisers identify issues before the inspection even begins.”
“Once a vehicle is in a shop bay, technicians can use the detailed fault data to streamline inspections, prioritize repairs, and ensure accurate documentation throughout the entire service and repair process,” Cooper added.
Fault code data from Diesel Laptops is also fed into the Pitstop management platform. The integration enables maintenance teams to anticipate and understand vehicle issues. According to the company, the AI-driven algorithms can produce an average time savings of 10 hours per week in diagnostic time.
See also: Industry knowledge hub grows
Improving safety with diagnostic data
TJ Thomas, director of marketing and customer solutions at Bendix, sees key safety value in diagnostic code data. “DTCs and messages from ADAS systems are getting more attention from fleets and telematics carriers to help verify that the safety systems are operational,” he said. “This can help fleets determine when systems go offline and a possible cause.”
“ADAS systems are starting to put out more prognostic-type information that makes it more straightforward for fleets to better optimize wear part replacement cycles,” Thomas added.
For example, Bendix’s newest generation of diagnostic software, ACom AE, covers all Bendix electronic systems and ECUs for ABS, ESP, Wingman Fusion, SmarTire, Intellipark, and other systems. Supported by Cojali and modeled on its Jaltest diagnostic software, Bendix ACom AE assists technicians when diagnosing and troubleshooting tractor and trailer electronic products and provides features like DTC reporting and bidirectional communication that enables configuration, calibration, and testing, Thomas explained.
When connected to a vehicle, Bendix ACom AE detects and gathers active and inactive diagnostic troubleshooting codes from Bendix and R.H. Sheppard electronic control units, as well as key ECUs, such as the engine and transmission.
For the Bendix AD-HFi air dryer with electronic pressure control, the company’s Electronic Air Control software provides diagnostics that help fleets get the most out of air dryers and cartridges. As part of the EAC software, air dryer status messages are provided via the J1939 network, with the capability to monitor excessive air demand, which could indicate leaks in the system.
“The software is programmed to know what a nominal duty cycle is for that compressor and how much air it should be producing so it can send a diagnostic code if something isn’t operating correctly,” Thomas explained.
Bendix also offers iSense Pro, which broadcasts rotor and pad life remaining percentages using pad wear sensing technology. The system reduces maintenance costs by continuously monitoring pad and rotor life at all wheel ends and alerting fleets via telematics when service is required, Thomas related. “Early detection of worn components helps prevent costly damage and enables fleets to proactively arrange optimal maintenance schedules,” he said.
Advantages for service providers and fleets
Across the board, for all makes and models of vehicles and their many systems and components, all-inclusive diagnostic tools have advantages for fleets and service providers.
TEC Equipment, a Portland, Oregon-based service provider with more than 35 locations, was using various OEM diagnostic tools, noted Jacob Klein, technical trainer. “As our customers started to diversify their fleets, we needed more information and a tool that could do everything,” he said.
“Implementing Noregon JPRO to scan all components on a vehicle, regardless of make and model, ensures we have visibility into all problems,” Klein continued. “It also allows us to work on a variety of vehicles without having to utilize various tools. As a result, this has allowed each of our shops to save money and reduce dwell time.”
One of the features of JPRO that TEC technicians use is Fault Guidance, an embedded troubleshooting application. “It’s a quick tool,” Klein said. “Once you’re hooked up to a vehicle, you click a button, then click which fault code you want to troubleshoot, and all the necessary information is there. That provides accurate and easy-to-follow troubleshooting steps and wiring diagrams, which has resulted in faster and more efficient service.”
About the Author
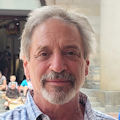
Seth Skydel
Seth Skydel, a veteran industry editor, has more than four decades of experience in fleet management, trucking, and transportation and logistics publications. Today, in editorial and marketing roles, he writes about fleet, service, and transportation management, vehicle and information technology, and industry trends and issues.